Technology Insight – Automated Robots With Heterogenous Networks
by Technische Universität Dresden
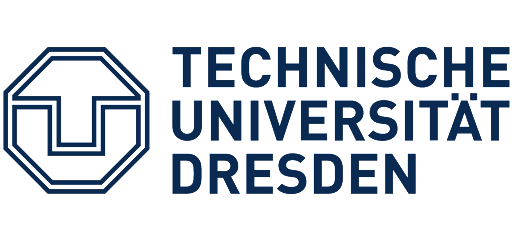
Introduction
Automation provides economic benefits for customers and service providers by improving the response time and increasing operational productivity. It facilitates the optimization of resource allocation and material utilizations, enabling lower production costs and creating opportunities for new services. Moreover, the consistency and reliability of services or products can be enhanced relaying on automatic measurements and testing. Furthermore, automation can be exploited to replace human workers in Hazardous environment or to perform risky experimentations.
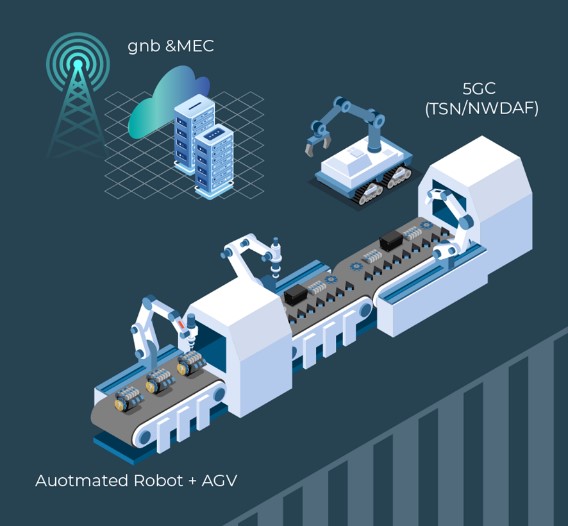
The majority of robots used in industrial automation are fixed and consist of jointed arms that performs specific tasks. Industrial networks are used to interconnect and control multiple robot arms in a factory production line. The control systems, such as the supervisory control and data acquisition (SCADA) architecture, comprise verities of sensors, actuators, controllers, human to machine interfaces (HMIs). In addition to supervisory computers for programming, network management and data collection. These entities are connected by means of an industrial network with real-time and deterministic communication capability.
Regarding connectivity, the state-of-the art industrial networks are primarily based on wired fieldbus systems and industrial Ethernet technologies. For involving mobile assets, such as automated guided vehicles (AGVs), wireless connectivity solutions based on WIFI and Bluetooth have also been investigated. However, these approaches are not sufficient to meet the ultra-reliability and low-latency communication (URLLC) requirements of critical mission and closed-loop control applications. This urges the development of new radio-access technologies (RAT) such as 5G-NR, which considers new air interface design to support URLLC use cases. In addition, time-sensitive networking (TSN) techniques are considered to achieve precise timing. The combination of industrial automation and traditional Internet of things (IoT) results in the definition of industrial IoT (IIoT). The IIoT relies on heterogeneous wired and wireless connectivity to interconnect diverse fixed and mobile devices with edge and cloud computing platforms. Moreover, by including the human-machine interaction via haptic system interface (HSI) and virtual and augmented reality (VR/AR) interfaces, and the tactile internet (TI) can be also integrated. Accordingly, this iNGENIOUS use case focuses on automated robot control in a wide sense considering:
- Open-loop control: which is typically, event-triggered, and may demand strong real-time connectivity with high reliability and bounded latency when safety is the concern.
- Closed-loop control: which bidirectional exchange between the controller and the device. This requires a strong real-time connectivity with high reliability and low jitter. Closed-loop control may also involve communication between different industrial controllers. Moreover, human-in-loop is another closed-loop control, where a human operator remotely interacts with real or virtual objects and feel the same experience as directly dealing with the corresponding physical entities. This requires HIS, such as haptic gloves and VR headset, to translate the human actions to machine type commands, and the machine feedback to human perceived signals.
IIoT Architecture
The IIoT system considered in INGENIOUS, as depicted in Figure 1, consists of devices, network infrastructure, and computational resources, which are used to implement network and management functions, and to run applications. The devices are diverse and range from simple IoT sensors to more complicated devices such as AGVs and robot arms as well as different type of HMIs. Each device is equipped with a connectivity module with certain access technology. The network infrastructure includes wireless access points (APs), gateways, and fixed network switches. Edge computation resources are deployed next to the APs to provide multi-access edge computing (MEC).
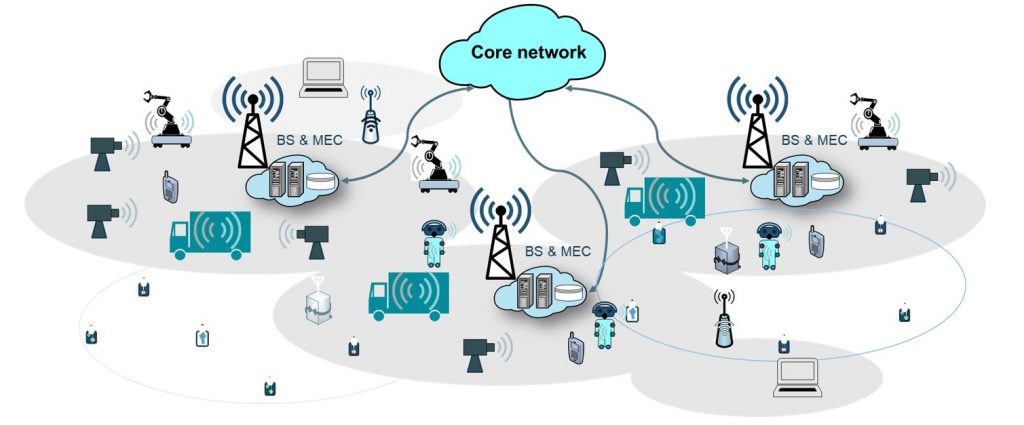
Different radio access technologies (RATs) are available for allowing the integration of commercial devices with heterogeneous connectivity solutions including 3GPP standards (4G, 5G), no-3GPP standards such as WIFI, Bluetooth, LoRa, in addition to flexible RAN that can be implemented by means of software defined radios. The core network is based on the 5G core and it provides logical control plane and data plane. In addition, the conventional industrial wired network can be connected to the wireless network at the IP layer as shown in Figure 2:
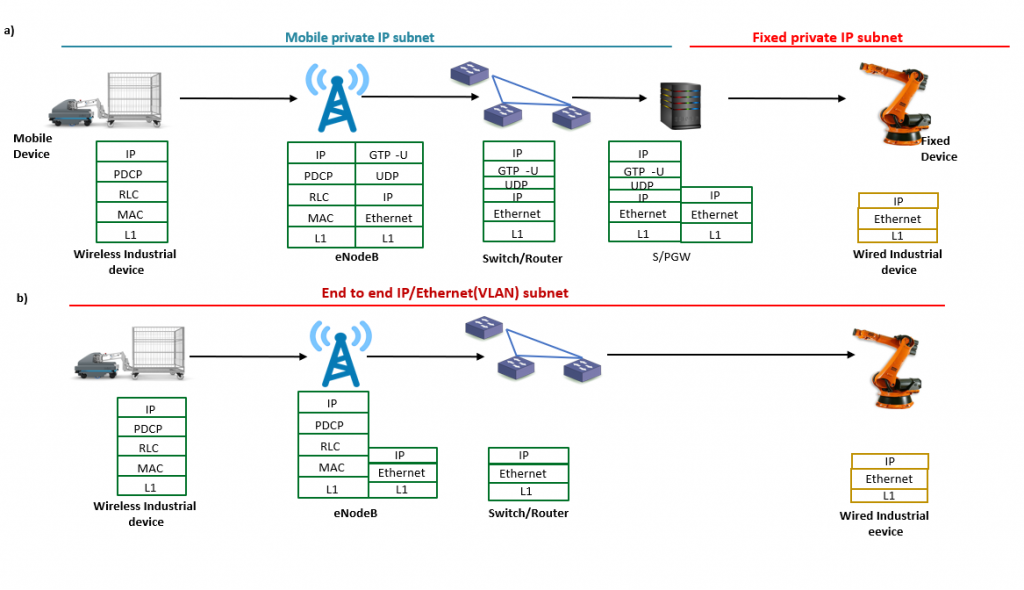
The network management and orchestration (MANO) provides coordination functionalities for the unified provisioning and operation of services at various levels that include network connectivity and applications. The involved hardware and software entities in the architecture are listed in Table 1.
Applications | End-user API, device drivers, control algorithms |
Technologies | SDN, MEC, TSN, NFV, MANO |
Core network | Control plane, data plane, 5G-Core, IP-network |
Access network | 5G-NR, 4G, WIFI, Bluetooth, LoRa, flexible RAN, Fieldbus, Ethernet |
Processing infrastructure | CPU, DSP, GPU, FPGA, desktops, laptops, servers |
Connectivity infrastructure | Switches, routers, radio frontend, baseband units, modems |
Devices infrastructure | Sensing: microphone, camera, RFID, environmental sensors, positioning sensors, etc. Actuating: switches, engines, robot arms, AGVs, etc. Human Interfaces: haptic gloves, VR headset, monitors, tablets. |
As a result, the IIoT system can be modelled with distributed computer architecture, as illustrated in Figure 3, where the MECs and the storage represent CPUs and memories, the devices correspond to the input/output (I/O) terminals, the network provides the computer bus, and the MANO plays the role of the operating system. The system hardware is abstracted, and application programming interfaces (APIs) are exposed for application development. In addition, device drivers are available to interact with devices for sending commands and acquiring data. In the ideal mode, all the resources in the system are connected and controller via the control plane by means of running services to monitor the connected devices, such as acquiring location information and operation status.

Application
The application is composed of closed-loop control threads that involve sensors, actuators, and controllers running on one or more MEC, as shown in Figure 4. In addition, human operator can interact with the application by means of a user interface. The connectivity and processing demands can be determined based on the application end-to-end (E2E) requirements in terms of latency, reliability, and packet rate.
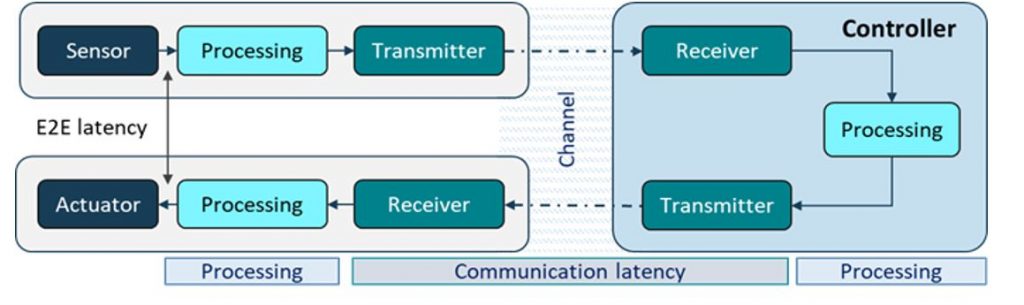
Prior to the execution, a set of networks and computing resources needs to be allocated and configured in the various network segments (RAN, edge, and core) to create seamless E2E communications . The orchestrator provides the required coordination functionalities to provision isolated logical network to interconnect and expose the requested devices. In practice, it provides E2E network slices for each required industrial service and related network communications. Once the resources are allocated, the application can enter the execution phase, where the TSN protocol ensures the synchronization among different nodes and support deterministic communications between devices that are registered as part of the TSN network. Moreover, during runtime phase, the E2E network slice is monitored by the MANO components to collect statistics and information about actual use and status of network and computation resources to enable slice optimizations. Status information is sent to the user interface. The operator can also modify the control loop parameters and send remote control commands.
When the job is done, all computational and network resources are released. The application phases are summarized in Table 2.
Analysis | Offline analysis by decomposing the application into control loops and defining the E2E requirements (latency, reliability, packet rate, and timing) for each loop. |
Ideal | Periodic devices status update on the control plane |
Initialization | Allocation of devices, processing resources, and setup of the network data plane (RAN resource allocation, and E2E slicing) |
Execution | Data exchange over the control loops and interaction with user interface. Monitoring of link qualities and failure detection. |
Termination | Close communications sessions, release computation and communications resources, and set devices to ideal mode |
Summary
In summary, this iNGENIOUS use case will contribute to the realization and testing of IIoT focusing on the following innovation areas:
- Software defined communications to facilitate the integration of multiple standards and allows new innovations to be implemented with existing hardware.
- Adaptive networking at all layers to fulfil wide range of services with different requirements.
- Time synchronization to integrate different technologies in heterogeneous network.
- Automated management and orchestration for faster deployment and running of applications.
- Application programming interface to simplify the application development and allows efficient reuse of devices and computational resources for multiple tasks.